introduction
「究極の電池」と呼ばれる「リチウム空気二次電池」を始めとする次世代電池の研究を進める成蹊大・齋藤研究室。2020年からCo-LABO MAKERを通じて企業からの受託実験や共同研究を行っています。「得られた研究成果だけでなく、企業の方々と共に行う研究は学生たちにも良い刺激となり、研究室を活性化するため仕組みの一つとしても機能している」と話す成蹊大・齋藤守弘教授に、Co-LABO MAKERの良さを聞きました。聞き手はCo-LABO MAKER代表の古谷です。
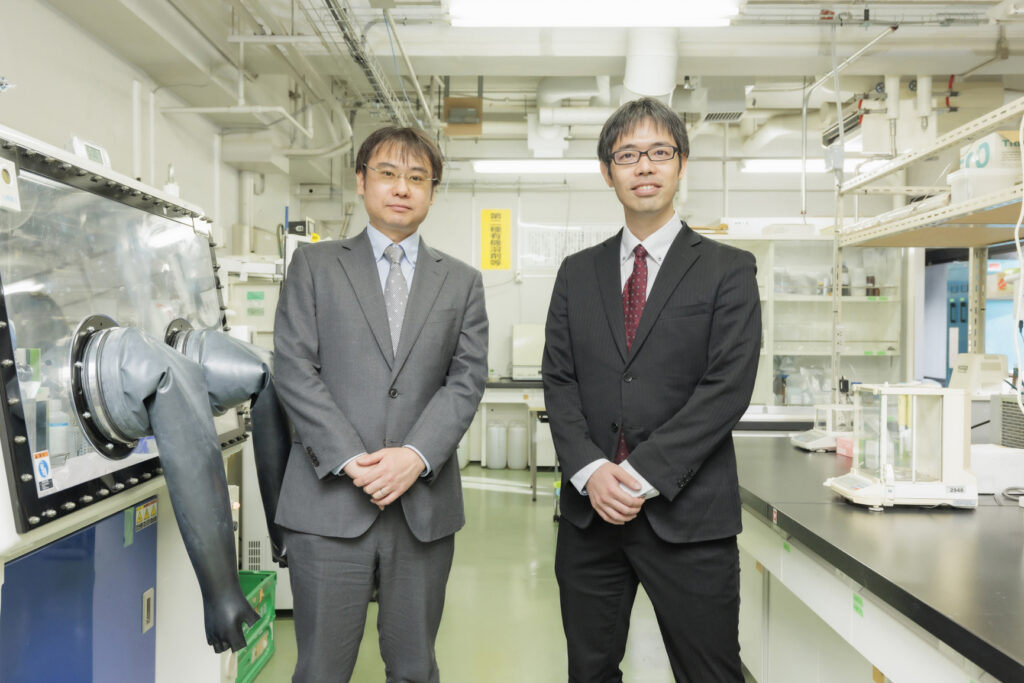
次世代電池を研究開発する成蹊大・齋藤研究室
古谷:まず、齋藤先生の研究について教えて頂けますでしょうか?
齋藤:ポストリチウムイオン電池となる「次世代電池の材料開発」を行っています。大きくは「リチウム”空気”二次電池」と、リチウム合金化シリコン負極を用いた「先進リチウム電池」の研究をしています。
「リチウム空気二次電池」は次世代電池のなかでも「究極の電池」と言われています。マイナス極にはリチウム金属を用い、プラス極には空気中の酸素を利用します。考えられるすべての電池のなかで最もエネルギー密度が高く、リチウムイオン電池のようなプラス極のコバルトなどのレアメタルが不要なため、電池の大幅な軽量化や低コスト化が可能になり、電気自動車用の駆動電源などに期待されています。
ただ、そのぶん解決すべき課題も多く残っています。例えば、リチウム空気二次電池は放電時に空気極上に生成するLi2O2を充電時に酸化分解するための過電圧が比較的大きく、すなわちエネルギー効率が低いと指摘されています。この解決のためには、結晶性が低く粒径の小さいLi2O2を生成しやすい環境を与える電解液や、Li2O2の酸化分解を促進するための電極触媒の開発が必要となります。
後者の電極触媒は、水を電気分解して水素を得るための電極触媒とも共通する点が多くあるため、いずれにも応用できる酸化マンガンナノシートをベースとした付加価値の高い電極触媒を合成し、「リチウム空気二次電池」と「水電解装置」の双方への応用を視野に入れて評価しています。
一方、リチウム金属負極にも課題があります。リチウム金属負極は放電時にリチウムイオンが電解液に溶解し、充電時には再度リチウム金属として析出します。この反応を繰り返すことで放充電を繰り返すわけですが、徐々にリチウム金属が針状に析出するため、正極と短絡する危険性が常にあります。そこで、これを回避するために代替材料としてリチウム合金化したシリコン負極の開発が必要なわけですが、我々の研究室ではシリコンを効率よく均一にリチウム合金化するための「リチウムプレドープ溶液」を開発しています。
この溶液を使うと、「リチウム空気二次電池」のような次世代電池用途のリチウム合金化シリコン負極や、「先進リチウムイオン電池」用途の初回不可逆容量のみを除去した安定なシリコン負極を簡便に作製することができます。
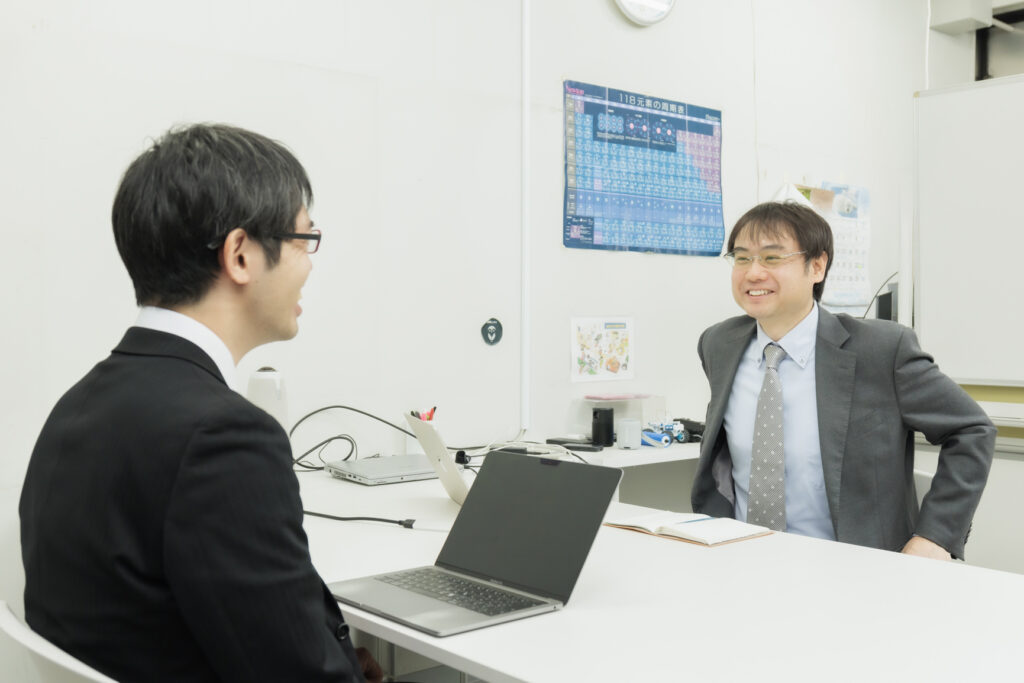
古谷:ちなみにリチウム空気二次電池はいつぐらいに実用化される目処なのでしょうか?
齋藤:最近では、トヨタ自動車が電気自動車用の全固体電池を2027年~28年を目処に実用化して、その後量産化すると発表していますね。そのような観点からは、私たちもここ2~3年の間にどの企業と組み、開発を加速して実用化へ向けていくかは考えていきたいと思っています。
古谷:この領域は私たちの生活に直結しており、エネルギー効率を大きく変える可能性がある研究ですよね。どんな展開になるかが楽しみです。
Co-LABO MAKERを受け入れて学生の学びが広がる
古谷:最初にCo-LABO MAKERをお使いいただいたのは、私からご連絡させて頂いた形でしたね。
齋藤:ええ。確か「初めは研究室で空いている部屋やドラフトを企業に貸して実験検討を進めつつ、技術相談にも乗って欲しい」という内容だったと思います。私たちも「面白そうだな」と思ってお話を受けてみました。
最初の受け入れは2020年でしたからコロナ禍の真っ只中でしたね。Zoomを繋いで、iPadで電池作製のためのグローブボックス内を映して、リアルタイムで相談しながら実験を進めていった記憶があります(笑)。
古谷:Co-LABO MAKERを通じて企業を受け入れて良かった点について教えてください。
齋藤:研究室の学生たちが非常に良い影響を受けていますね。学生は、普段なかなか企業の、しかも実際に電池開発に携わっている方々と接する機会は少ないもの。このような研究者の方々が研究室にいらっしゃると、研究を通じて学生たちとも交流が生まれて雰囲気がピリッとします。学生たちも、今ここで勉強している内容が将来どのようにビジネスに役立っていくのかが見えると、研究へのモチベーションアップにも繋がります。
また、外国籍の方がいらっしゃる場合もあるわけですから、そのときは英語でコミュニケーションを取らなくてはいけません。その結果、必要に迫られて、語学を勉強することになります。旧帝大の研究室では、常に企業との共同研究が走っているので珍しくない光景ですが、中堅私立大ではそこまで数が多くありません。これらの効果を考えると、もっとCo-LABO MAKERを通じた企業の受け入れは増やしたいですね。
古谷:確かに。東北大学では企業との共同研究は常に何社か入っており、私自身も刺激を受けていました。その環境がどの大学でも当たり前になるといいですね。
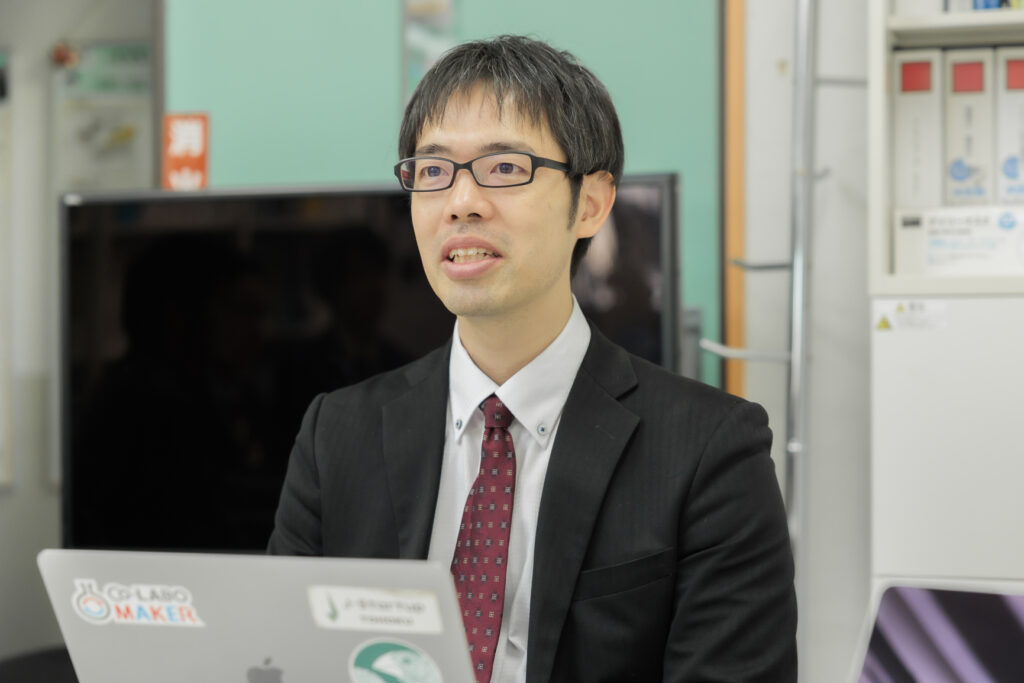
齋藤:一方で、企業にとっては自社の新しい開発材料を用いて研究をしようとすると、どうしても社内の設備では間に合わないといったこともあると思います。試験的で少量であっても実験後の廃液などをどうするか、といった問題もよく耳にします。そのような場合にも、大学であれば設備が整っていますから対応ができます。「ちょっと実験をしたい」というとき、企業にとってはCo-LABO MAKERを使うメリットは大きいですね。我々の研究室でも電池材料であれば、多くの場合、受け入れ可能ですのでお気軽に声をかけて頂ければと思います。
企業さんからの新しい材料の持ち込みで「何か電池に使えませんか?」、「こんな独自技術を持っているのですが、電池の性能アップに繋がりますか?」という提案は、私たちの知見としても重要ですし、その提案を受けるにあたって研究室のなかで工夫を凝らすということもありますし、我々自身の技術レパートリーも増やす意味でも非常にありがたいですね。
古谷:新しい材料や実験方法を開拓していくことは本当に有益ですよね。
齋藤:私自身の経験でも「実はこんな方法もあったんだ」という引き出しの多さは極めて大事なことだと思っています。
例えば、NMRは一般的には有機分子の化学構造を決定するために使いますよね。でも、私の場合、博士後期課程修了後、つくばの産業技術研究所に2年間特別研究員として働いていたんですが、そのときの恩師に教えていただいたのは、電解液中の溶媒分子やイオンの自己拡散係数を測定する方法でした。だから、当時の私自身はNMRのイレギュラーな使い方から先に教わりました(笑)。とはいえ、この方法をマスターしたことで電解液中のリチウムイオンがどれくらいの速さで動いているかや、溶媒との相互作用のなかでどう動いているのかを見ることができました。当時は、固体高分子形燃料電池のナフィオンなどの電解質膜中のイオンや水分子の拡散挙動についても研究していましたので、これらの物質輸送のイメージが広がりましたし、新しい使い方を知るとアイデアも増えますよね。
その後も、大学を渡り歩いたり、他の研究室にも沢山お邪魔させてもらい、それぞれの研究室でどんな実験装置を使って、どのように研究を進めているのかを見せていただいたりもしました。自分の専門以外の分野にも色々と興味を持っていると、ふとしたときに後で引き出しとして使えることが多々あります。
もっと言えば、各人が広く化学に関連することを知っておくことも勿論大事ですし、実際に材料開発をしていく上では、資源やコストなどの面から、地政学的視点や、政治的視点、更には世界情勢等を知っておくことも重要です。そのような中で、今後、日本の電池産業がどのような方向へ進み、そこへ産官学それぞれの研究者一人ひとりがどのような形で寄与していくかを常に考えることが大切なことだと思います。
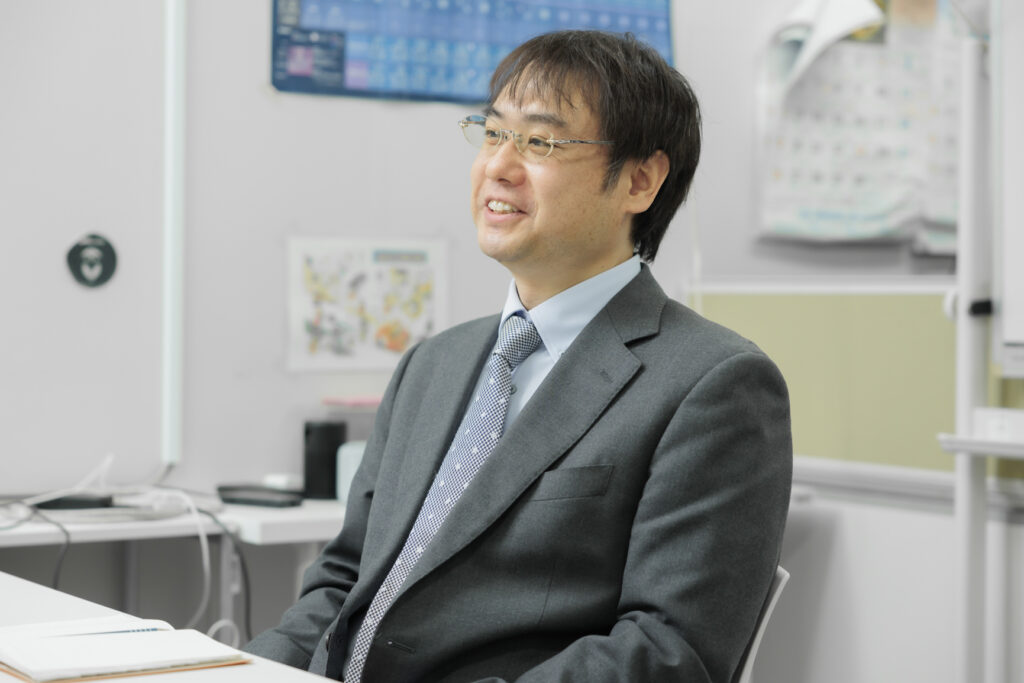
古谷:各メーカーはトレンドの一番大きな流れを追い「とにかく一番先頭を走れば勝てる」という発想で研究開発をしていたりしますよね。ところが、昨今ではその発想では勝てない。コアの技術があった上で何かを組み合わせて新しい時代のニーズに適応したプロダクトを作ることが今求められていますね。
研究を通じて日本の発展に貢献する
古谷:齋藤先生の今後の展望についてもお聞かせ下さい。
齋藤:現在は一番ハードルが高いと言われている電気自動車向けの次世代電池を中心に研究していますが、モビリティも多様化していますし電動バイクなどの二輪系や空飛ぶクルマ、ドローン、スマートウォッチ、スマートグラスなど新しい中小型・モバイル機器など、将来需要が拡大されると思われる新しい用途も視野に入れた“電池研究”を続けていきたいですね。
あとは、大学としては人材育成です。研究室から自動車メーカーや関連する化学・材料メーカーに就職する学生も増えています。電池について深く学んだ多くの人材が電池を含め、電気化学デバイスに関連する企業へ就職する。また、OB・OGとして会社説明会や共同研究の相手先企業として研究室へ戻ってくる。このサイクルを回すことで、研究室や大学、ひいては日本の発展にも貢献できると思っています。
古谷:Co-LABO MAKERで受け入れた企業との共同研究がきっかけとなり、学生さんがその企業に就職し、関係性が続く例もあるそうですね。そんな事例をもっと増やせるように、Co-LABO MAKERも貢献していきたいです。今日はありがとうございました。